An air assist is a needed accessory for a laser cutter that my K40 did not include. An air assist does a few things. It helps blow away bits of carbon out of the way so the laser is more effective at cutting through the material and it keeps a flame from forming which makes black smoke that fouls up the lens, blocks the laser from cutting the material, and instead heats the lens– eventually damaging it.
The few things I have cut usually resulted in me lifting up the lid to blow on the laser point because when the carriage was traveling in a certain direction the flame would ride right up against the plastic bearings. Also, the lens needed to be removed and cleaned with nearly every use or it would block the beam to the point it was not effective.
The first thing I needed was an air supply. It doesn’t take a lot of air and I didn’t want to deal with the noise of a compressor, so I went with a large aquarium aerator. The Active Aqua AAPA70L supplies plenty of air and the sound is hardly noticeable along with the water pump and steppers.
To deliver the air people have either put a bent piece of tubing to the side aimed at the general location or created a nozzle that fits over the lens and directs the air straight down into the piece. The later has the benefit that the lens being sounded by positive pressure so it’s pretty much impossible for the smoke to come into contact with it.
There were some plans on Thingiverse, but I don’t have a 3D printer. Prints of a couple of those were being sold on eBay, but the quality looked terrible– which is why I do not have a 3D printer.
Then I found plans from Bart Dring (of MakerSlide fame) as well as a blog of another who turned a metal one on a lathe.
I have a Mini Lathe. I could make my own.
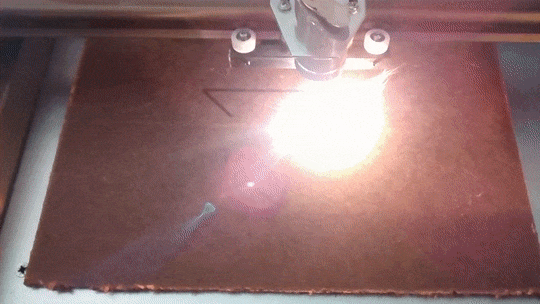
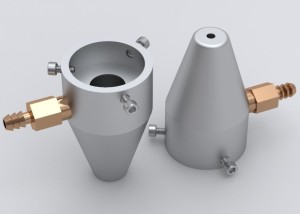
I did some measuring on the carriage and realized the one from Bart Dring would fit the laser lens (it was designed for the same one) but it would interfere with the rails the bearings were mounted too.
I didn’t have a piece of material suitable so I ordered some 6061 1-1/4″ round bar. I also ordered some better tools for the lathe that I already indented to have– An OXA quick-change tool post, 3/8″ indexable insert cutters, and a boring bar set.
The ability to position the calipers in the laser was limited so I was not very confident in the precision of my measurements. I made a piece to check. I chucked up an old aluminum “cupcake” ingot that’s been aging in my basement for a few years
I finalized the dimensions and it was time for the real thing.